Eye on Efficiency: Unleashing the Potential of PLC-Vision Integration
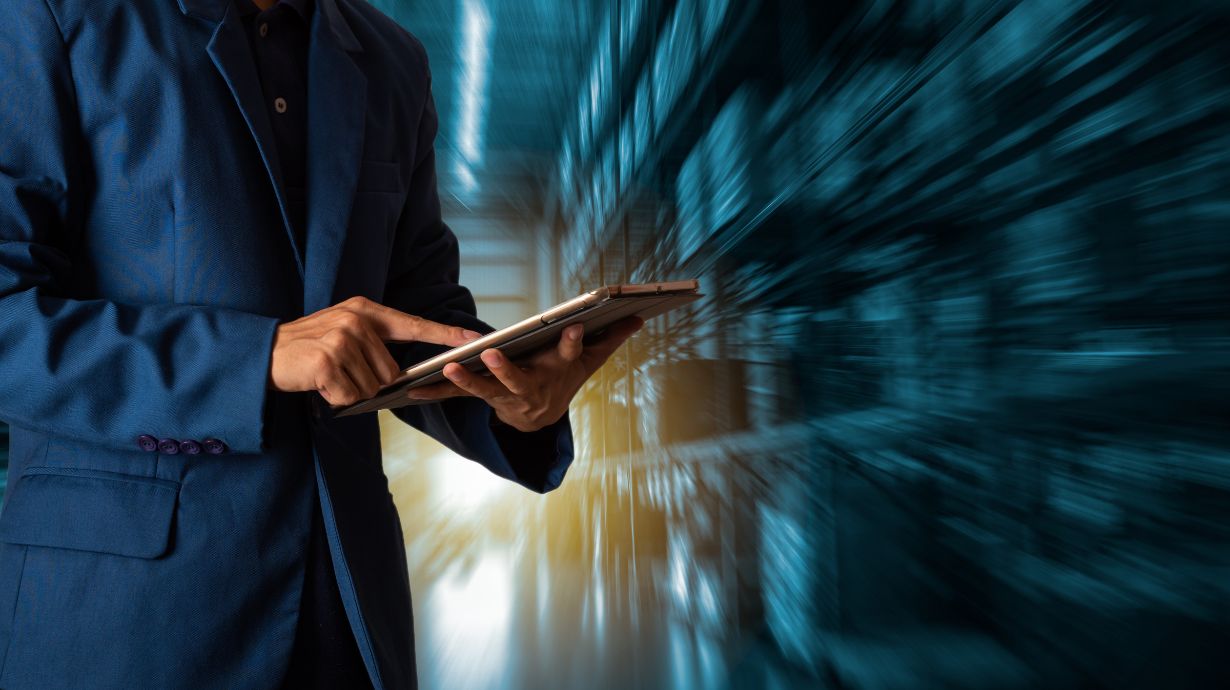
Cameras and other vision systems are often used for visual inspection and quality assurance in a wide variety of industries. Programable-logic-controller (PLC) programming can act as the bridge between the "eyes” of these vision systems and the "hands” of your automated line. But how does the process work and why is it beneficial?
Camera systems provide clear, real-time visual information that is relayed through a series of algorithms, giving you intelligent and accurate control. Here is how the process works:
- Your vision system’s cameras/sensors collect visual data in the form of images and videos.
- Communication protocols such as Ethernet/IP, Modbus TCP/IP and Profinet transfer this visual data to the PLC through dedicated ports and networks.
- Images are analyzed using pre-programmed algorithms that perform tasks such as code reading, defect detection, and object recognition.
- The results of this analysis are interpreted by PLC program, typically as numerical values or binary pass/fail codes, and control-based action is taken based on the result. For example, the system may, adjust machine settings, reject a faulty or damaged product, or trigger the movement of a robot or cobot to a specific location.
Through consistent and efficient visual inspection, you can ensure the reliability of your processes and quality of your product. This real-time data collection and analysis eliminates manual inspection tasks and optimizes production flow, reducing downtime and errors. Plus, PLC programs can be customized for specific applications and easily adapted to changes in your production environment. Before implementing your first PLC-Vision integration, here are a few things to consider:
Cameras/Sensors: Choose the right resolution, frame rate, and lens for your inspection needs.
PLC: Make sure you have enough processing power and communication ports for the job.
Environment: Ensure that your workspace is an appropriate temperature for the job, and that you have appropriate power supplies and lighting to accommodate your vision system.
Scalability: Consider potential needs for additional cameras or processing power in the future.
User Interface: Keep it intuitive for easy configuration and troubleshooting.
Programming Language: Pick one familiar to your team and compatible with your PLC.
Vision Algorithms: Select the right tools for your specific inspection tasks.
Security: Implement security measures to protect against unauthorized access and data tampering.
Support and Maintenance: Choose software with reliable support and maintenance options for troubleshooting and updates.
Physical Inspection: Check the full system for proper connections and power.
Functional Testing: Simulate camera inputs and verify the PLC's response.
Performance Evaluation: Measure speed, accuracy, and consistency of the system.
User-Experience Testing: Get feedback from operators to ensure smooth operation.
With careful planning and thoughtful implementation, PLC-vision integration can quickly improve the quality and efficiency of your production line. Ditch the guesswork and let PLC programming guide you to a brighter, more efficient future!
Want to learn more about specific camera, sensor, and PLC system options? The Triad Technologies Automation Team is here to help! Contact us and let our experts guide you through your vision system journey, or visit our automation lab in Sharonville to help qualify products and PLC-vision system solutions before you buy. Lab visits are by appointment only – schedule today!